Технология электрической сварки металлов и сплавов плавлениемАппаратура для полуавтоматической сварки плавящимся электродом
При полуавтоматической сварке механизирована только операция подачи электродной проволоки, а передвижение дуги вдоль свариваемого шва осуществляется вручную (рис 8 3) Для того чтобы полуавтоматическая сварка могла успешно соперничать с прогрессивными методами ручной сварки, она должна сочетать преимущества автоматической сварки с маневренностью, универсальностью и гибкостью ручной
Высокие эксплуатационные свойства современных сварочных полуавтоматов достигаются за счет применения тонкой электродной проволоки, подаваемой к электрической дуге по гибкому направляющему каналу, который позволяет разместить относительно
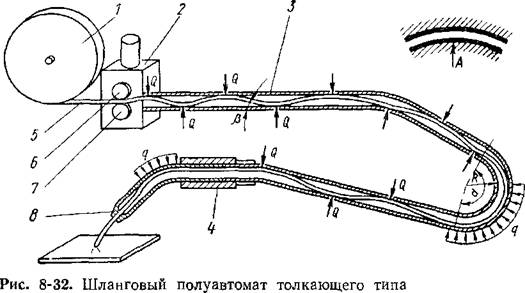
тяжелый механизм для подачи проволоки на значительном расстоянии от зоны сварки, где расположен только рабочий орган — сварочная горелка 4 (рис. 8-32).
При сварке тонкой проволокой на больших плотностях тока (до 200 А/мм2) процесс саморегулирования дуги происходит чрезвычайно интенсивно. Это дает возможность при ручном перемещении горелки использовать независимую скорость подачи. Случайные колебания длины дугового промежутка, связанные с неточностью ручного ведения электрода, как правило, легко компенсируются саморегулированием дуги.
Сварочный полуавтомат (рис. 8-32) содержит катушку с проволокой /, подающее устройство 2, гибкий направляющий канал 3 и ручной держатель или горелку 4. Элактродная проволока 5 сматывается с катушки и проталкивается ведущим 6 и прижимным 7 роликами через канал и горелку в дугу. В канале проволока находится в сжатом состоянии; усилие сжатия изменяется от максимального при входе в канал до нуля в наконечнике 5 горелки. Вследствие сжатия проволока располагается в канале в виде волнообразной змейки с переменным шагом волн. В местах контакта проволоки с каналом возникает сила трения Q, величина которой тем больше, чем больше угол (5 и чем больше число точек контакта проволоки с каналом.
Сопротивление проталкиванию проволоки зависит от изгиба гибкого направляющего канала с проволокой (сила Л), от его длины и от материала трущихся поверхностей. На закруглениях со сравнительно небольшим радиусом (R) проволока укладывается как бы по внутренней поверхности желоба шкива, создавая дополнительное трение q, величина которого зависит от угла обхвата а. Таким образом, сопротивление проталкиванию проволоки имеет комбинированный характер. Для тонких проволок решающее значение имеет потеря продольной устойчивости, для толстых — усилие изгиба.
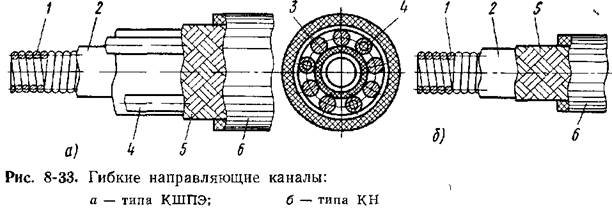
С возрастанием внешнего механического сопротивления (изгиб, прихватывание в наконечнике и др.) возрастает частота волн и, следовательно, сопротивление движению. Поскольку величина внешнего сопротивления не является постоянной, то и проволока может подаваться с переменной скоростью. Это особенно ощутимо в тех случаях, когда оболочка канала обладает малой жесткостью в продольном направлении.
Направляющие каналы любой конструкции (рис. 8-33, а я б) состоят из трубки / (монолитной или в виде спирали), защитного слоя 2, концентрично расположенной оболочки 5, которая препятствует растяжению внутренней трубки, и наружного защитного слоя 6. В ряде случаев трубку можно вынимать из оболочки. В каналах типа КШПЭ (рис. 8-33, а) вокруг спирали размещены токоведущие жилы 3 и провода управления 4.
Для порошковых проволок, проволок из титана и алюминия сопротивление проталкиванию намного выше, чем для стальных проволок сплошного сечения, что требует значительного увеличения силы проталкивания подающего механизма. Это часто приводит к деформации проволоки и к ее поломке у входа в канал. Для снижения сопротивления проталкиванию применяют каналы, изготовленные из материалов с малым коэффициентом трения, или обычные каналы, смазанные нейтральной смазкой (например, дисульфидом молибдена). Последний снижает сопротивление проталкиванию в 1,5—2 раза. Применение спиралей из бронзы снижает это сопротивление в 2—3 раза, спиралей из фторопласта— в 6—10 раз. Однако каналы из синтетических материалов дороги, поэтому их применение целесообразно только в исключительных случаях (сварка алюминия, титана и др.)-
Для мягких проволок или проволок из металла с высоким коэффициентом трения, а также для проволок малого диаметра (менее 0,8 мм) полуавтоматы толкающего типа неприменимы. В этом случае применяются полуавтоматы тянущего типа, т. е. с механизмом подачи, расположенным в рукоятке горелки (рис. 8-34). Однако при наличии двух-трех изгибов, что неизбежно при длинном шланге и большой зоне обслуживания, сопротивление движению проволоки вследствие силы трения q резко возрастает.
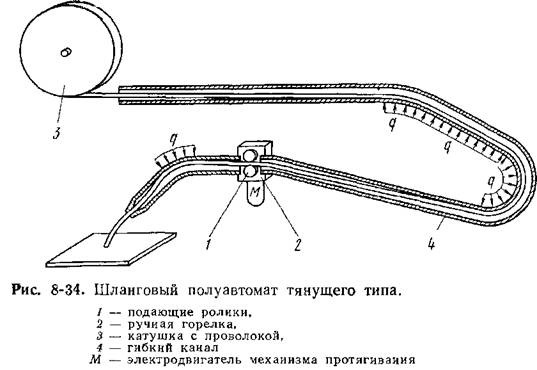
Поэтому должна быть увеличена мощность привода механизма подачи, что приводит к утяжелению горелки.
Сварку со шлангами большой длины можно осуществлять путем применения так называемых систем тяни-толкающего типа (рис. 8-35). Они содержат механизм подачи /, проталкивающий проволоку через канал 3, и тянущий ее механизм 2 При такой схеме подачи в канале устраняется волнообразное расположение проволоки, снижается число точек трения между проволокой и каналом.
Условием работоспособности систем тяни-толкающего типа является равенство скоростей подачи в тянущем и толкающем 1>2 механизмах. Поскольку обычными средствами это достигается трудно, как правило, один из приводов (например тянущий) должен иметь очень мягкую характеристику, т. е. в зависимости от нагрузки частота его вращения должна изменяться в широких пределах, а скорость подачи проволоки в этом механизме должна быть несколько большей, чем в толкающем. В результате проволока будет находиться в натянутом состоянии. Скорость ее подачи толкающим механизмом будет определять число оборотов тянущих роликов вследствие снижения частоты вращения привода с мягкой характеристикой (например пневматического).
Размещение тянущего механизма в ручной горелке излишне ее утяжеляет. Поэтому такие устройства применяют в исключительных случаях.
Забиваем Сайты В ТОП КУВАЛДОЙ - Уникальные возможности от SeoHammer
Каждая ссылка анализируется по трем пакетам оценки: SEO, Трафик и SMM.
SeoHammer делает продвижение сайта прозрачным и простым занятием.
Ссылки, вечные ссылки, статьи, упоминания, пресс-релизы - используйте по максимуму потенциал SeoHammer для продвижения вашего сайта.
Что умеет делать SeoHammer
— Продвижение в один клик, интеллектуальный подбор запросов, покупка самых лучших ссылок с высокой степенью качества у лучших бирж ссылок.
— Регулярная проверка качества ссылок по более чем 100 показателям и ежедневный пересчет показателей качества проекта.
— Все известные форматы ссылок: арендные ссылки, вечные ссылки, публикации (упоминания, мнения, отзывы, статьи, пресс-релизы).
— SeoHammer покажет, где рост или падение, а также запросы, на которые нужно обратить внимание.
SeoHammer еще предоставляет технологию Буст, она ускоряет продвижение в десятки раз,
а первые результаты появляются уже в течение первых 7 дней.
Зарегистрироваться и Начать продвижение
В соответствии с назначением полуавтоматы бывают : 1) стационарными (рис. 8-36, а), где в одном блоке сосредоточены источник питания, аппаратура управления, механизм подачи

проволоки, держатель со шлангом, в ряде случаев газовая аппаратура, автономная система охлаждения, фигурка с проволокой и т. д. Зона обслуживания такого полуавтомата лимитируется длиной шланга; 2) передвижными (рис. 8-36, б), состоящими из двух блоков; в одном размещен источник питания, пускорегу-лирующая и другая громоздкая аппаратура, во втором — тележка с механизмом подачи, бухтой для проволоки, держатель со шлангом. Тележка передвигается на колесах или переносится. Зона обслуживания лимитируется длиной гирлянды проводов и длиной шланга; 3) легкими, переносными (рис. 8-36, в) они снабжены легким подающим механизмом и малой катушкой с проволокой; 4) шпулечного типа (рис. 8-36, г), предназначенные для сварки в защитной газовой среде, под флюсом или открытой дугой без внешней защиты.
Различают полуавтоматы для сварки под флюсом, в среде инертных или защитных газов, а также открытой дугой без флюсовой или газовой защиты (табл. 8-6). Наибольшее распространение получили аппараты для полуавтоматической сварки в защитной газовой среде. По сравнению со сваркой под флюсом такие
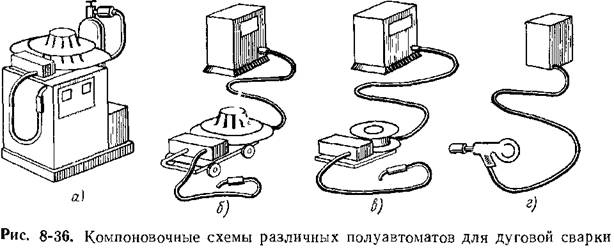
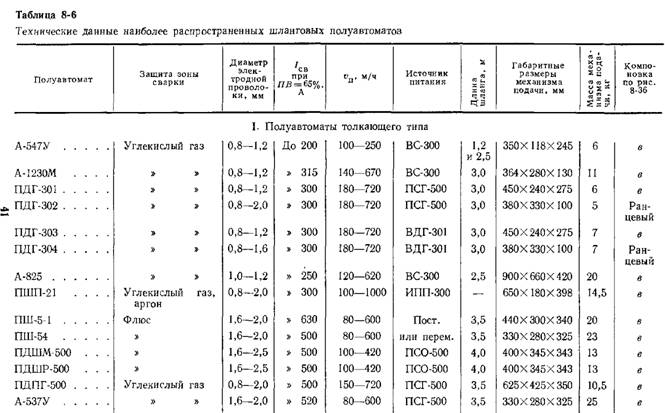
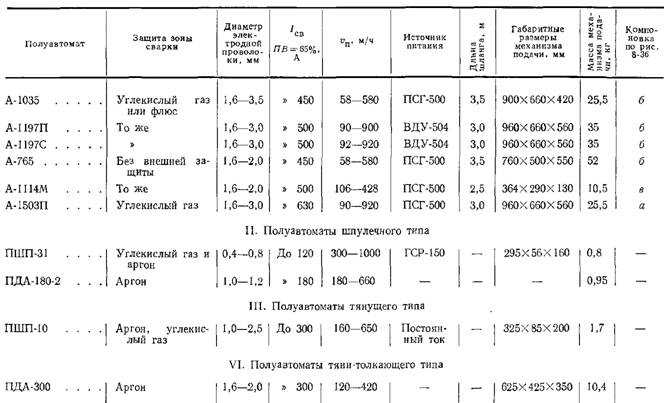
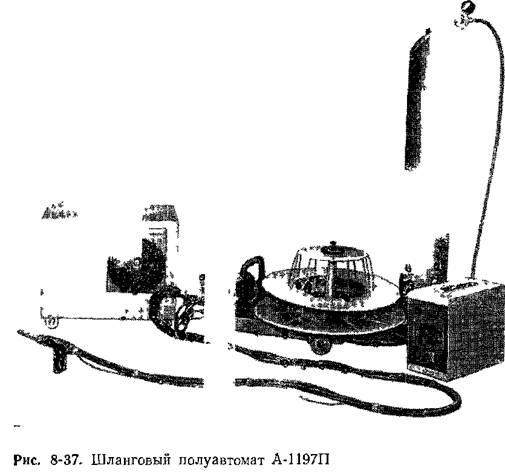
полуавтоматы обеспечивают возможность наблюдения во время работы за сварочной ванной, возможность сварки швов с различным положением в пространстве. Горелка таких полуавтоматов легче и маневренней, чем при сварке под флюсом.
На рис. 8-37 показан полуавтомат А-1197П для сварки в углекислом газе сплошной и порошковой проволоками на токе силой до 500 А. Аппарат снабжен механизмом подачи с двумя парами ведущих роликов на передвижной тележке, на которой расположена также фигурка для проволоки. Рабочий инструмент полуавтомата — горелка (рис. 8-38) содержит изогнутый мундштук 5 с переходной втулкой 2 и наконечником 6, рукоятку / с гашеткой 4 пусковой кнопки, защитный щиток 7 и сопло 5 для создания вокруг зоны сварки защитной атмосферы 9. Сопло электрически изолировано от наконечника и может легко заменяться. Переходная втулка имеет ряд отверстий 3, расположенных перпендикулярно направлению подачи проволоки и предназначенных для подвода в зону сопла защитного газа. Это обеспечивает получение ламинарного газового потока.
При сварке в углекислом газе выделяющиеся брызги прилипают к соплу и наконечнику, ухудшая газовую защиту зоны сварки и образуя токоведущую перемычку между соплом и
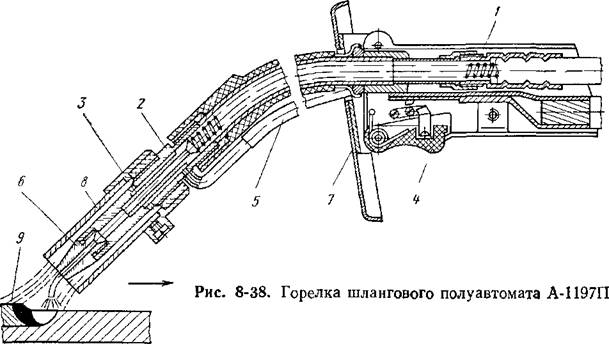
наконечником горелки. Для снижения вероятности прилипания брызг применяют охлаждаемые сопла, составные с изоляционной прокладкой, металлокерамические и др. Несколько снижают прилипание брызг теплостойкие покрытия или хромирование сопла. Эффективно применение защитных смазок, например силиконовых (раствора кремнийорганических соединений). При наличии смазки на поверхности сопла и наконечника брызги металла не привариваются, а только прилипают и потом легко удаляются.
Горелки для сварки под флюсом, конструкция которых аналогична рассмотренной конструкции горелки полуавтомата А-1197П (рис. 8-38), снабжены небольшой воронкой, из которой флюс поступает в сопло под действием собственного веса. Для лучших условий ссыпки флюса воронка может поворачиваться вокруг оси наконечника.
Наряду с универсальными выпускаются специализированные полуавтоматы, например мощные полуавтоматы для заварки дефектов чугунного литья, полуавтоматы ранцевого типа для сварки в условиях монтажа (механизм подачи и катушка расположены в ранце на спине сварщика), полуавтоматы для сварки определенных типов изделий и т. п.
|