Технология термической обработки металловДетали подшипников
Общие сведения. Наряду с высокими точностью обработки и качеством отделки рабочих поверхностей металл для деталей подшипников качения и термическая обработка их являются основными факторами, определяющими срок службы подшипников. При работе подшипников качения кольца, шарики и ролики подвергаются: а) воздействию высоких удельных нагрузок переменного характера, вследствие чего в металле возникают явления усталости, в частности развивается контактное выкрашивание; б) износу от трения; в) химическому износу вследствие контакта с атмосферой или смазкой, содержащей примеси; г) абразивному износу; д) напряжениям от раздавливающей нагрузки.

и ШХ15СГ (0,95—1,05% С; 1,30—1,65% Сг; 0,9—1,2% Мп; 0,40—0,65%о 31); в обеих сталях содержится не более 0,02% 3 и 0,027% Р. После ковки структура стали — пластинчатый перлит и тонкая разорванная карбидная сетка (рис. 160), твердость НВ 255—340, обрабатываемость стали с такой структурой и твердостью затруднена.
Для снижения твердости до НВ 178—207 и получения структуры зернистого перлита, обеспечивающей хорошую обрабатываемость, заготовки подвергают отжигу при 780—800° С с последующим медленным охлаждением (15—25° С/ч) в интервале температур
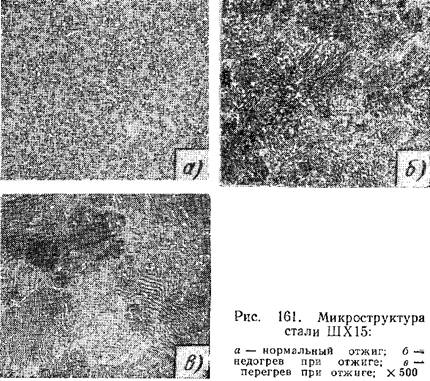
приводит к образованию крупнозернистого перлита; такая структура обладает низкой твердостью, но неблагоприятна для последующей закалки. Нормальной структурой после отжига является структура мелкозернистого перлита (рис. 161, а). При недогреве при отжиге сохраняется часть тонкопластинчатого перлита (рис. 161, б), а при перегреве образуется структура крупнопластинчатого и зернистого перлита (рис. 161, в).
На процесс закалки подшипниковых деталей влияет хром. Хром увеличивает количество избыточных карбидов в структуре стали и уменьшает чувствительность к перегреву. Вследствие присадки хрома уменьшается критическая скорость закалки и увеличивается прокаливаемость. Небольшая критическая скорость закалки необходима для того, чтобы можно было детали закаливать в масле. При закалке в масле происходит частичный отпуск мартенсита, что снижает напряжения.
С увеличением содержания хрома критическая скорость закалки значительно понижается. Для стали ШХ15 (1% С и 1,5% Сг) по сравнению со сталью У10 (1% С) критическая скорость закалки уменьшается с 500 до 35—40° С/с. В связи с уменьшением критической скорости закалки детали из стали ШХ15 прокаливают на значительно большую глубину по сравнению с деталями из стали V10.
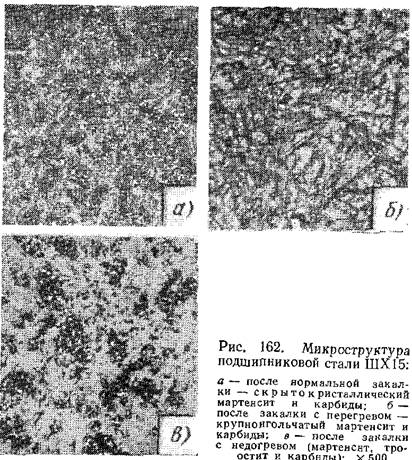
Температура закалки подшипниковых сталей колеблется в пределах 790—870° С в зависимости от массы деталей: чем крупнее деталь, тем выше температура закалки. Охлаждение проводится в масле (кольца, ролики) или в растворе соды, или поваренной соли в воде (шарики). После закалки и отпуска твердость HRC 62—65. Оптимальной структурой закаленной подшипниковой стали является скрытокристаллический мартенсит с равномерно распределенными мелкими избыточными карбидами (рис. 162, а). Структура игольчатого и крупноигольчатого мартенсита с карбидами (рис. 162, б) является признаком перегрева. Детали подшипников, закаленные с подогревом, имеют пониженную прочность. Структура мартенсита с участками троостита и карбидами (на рис. 162, в) характеризует недогрев или замедленное охлаждение при закалке. Такая структура обладает пониженной твердостью и поэтому является недопустимой. Важной характеристикой качества закалки является вид излома. Наилучший излом — шелковистый, фарфоровидный. Излом с заметной зернистостью является признаком перегрева стали. Занозистый излом характеризует неполную закалку стали.
Термическая обработка подшипниковых колец. Для колец диаметром до 200 мм, изготовленных из стали ШХ15, темпера* тура нагрева находится в пределах 820—870° С в зависимости от средней толщины стенки кольца. Чем больше толщина стенки, тем выше температура нагрева. Продолжительность выдержки (от 25 до 70 мин) устанавливается в зависимости от толщины стенки колец.
Кольца самых маленьких подшипников нагревают в электропечах в атмосфере защитного газа. Кольца малых и средних подшипников обрабатывают в конвейерных газовых или электрических печах, в печах с вращающимся подом или в соляной (цианистой) ванне. Несколько соляных ванн, имеющих разные температуры, могут быть установлены последовательно друг за другом.
Нагретые до температуры закалки кольца охлаждают в индустриальных маслах И20, И12, ИС20, ИС12 при температуре 30— 60° С. После закалки кольца промывают в 3—5%-ном содовом растворе (70—90° С) и подвергают отпуску (не позднее 3 ч после закалки) при 150—160° С в течение 1,5—2 ч. Для устранения роста кольца прецизионных подшипников целесообразно подвергать обработке холодом (перед отпуском) по режиму: закалка-промывка—обработка холодом—отпуск.
Термическая обработка шариков и роликов. Высокие требования, предъявляемые к твердости и однородности структуры на поверхности шариков и роликов, заставляют внимательно относиться к выбору закалочного оборудования. Наилучшими агрегатами для нагрева под закалку шариков и роликов мелких и средних размеров (шариков диаметром до 50 мм и роликов диаметром до 30 мм) являются барабанные печи (с вращающимся муфелем). В них шарики и ролики движутся поступательно и вращаются, что обеспечивает равномерный нагрев.
Крупные шары и ролики (диаметром до 70—75 мм), изготовляемые из стали ШХ15СГ, нагревают на противнях в конвейер* ных печах. Крупные шары (диаметром 75—200 мм) нагревают в двух соляных ваннах; одна из них служит для предварительного нагрева (780—800° С), а другая для окончательного нагрева (840—890° С).
Охлаждающими средами при закалке шариков и роликов являются масло, водные растворы соды (Ыа2СОэ и ЫаС1).
Ролики диаметром более 12 мм охлаждают или в масле, или, если они изготовлены из стали ШХ15, допускается охлаждение в 5— 7%-ном содовом растворе. Шарики и ролики диаметром более 50 мм охлаждают на специальных качающихся приспособлениях.
Забиваем Сайты В ТОП КУВАЛДОЙ - Уникальные возможности от SeoHammer
Каждая ссылка анализируется по трем пакетам оценки: SEO, Трафик и SMM.
SeoHammer делает продвижение сайта прозрачным и простым занятием.
Ссылки, вечные ссылки, статьи, упоминания, пресс-релизы - используйте по максимуму потенциал SeoHammer для продвижения вашего сайта.
Что умеет делать SeoHammer
— Продвижение в один клик, интеллектуальный подбор запросов, покупка самых лучших ссылок с высокой степенью качества у лучших бирж ссылок.
— Регулярная проверка качества ссылок по более чем 100 показателям и ежедневный пересчет показателей качества проекта.
— Все известные форматы ссылок: арендные ссылки, вечные ссылки, публикации (упоминания, мнения, отзывы, статьи, пресс-релизы).
— SeoHammer покажет, где рост или падение, а также запросы, на которые нужно обратить внимание.
SeoHammer еще предоставляет технологию Буст, она ускоряет продвижение в десятки раз,
а первые результаты появляются уже в течение первых 7 дней.
Зарегистрироваться и Начать продвижение
После закалки шарики и ролики подвергают отпуску (не позже 3 ч после закалки) при 150—160° С с выдержкой в течение 2—6 ч (в зависимости от диаметра). Твердость после закалки и отпуска HRC 62—65, а микроструктура — скрытокристалли-ческий мартенсит и карбиды.
Термическая обработка деталей подшипников из цементуемой стали. Для изготовления деталей крупногабаритных подшипников (диаметром более 400 мм) применяют стали: ШХ15СГ — для подшипников, работающих при малых нагрузках, и цементуемую сталь 20Х2Н4А — для подшипников, работающих в тяжелых условиях при больших ударных нагрузках.
Детали крупногабаритных подшипников (кольца, ролики), изготовленные из стали 20Х2Н4А, подвергают глубокой цементации с получением цементованного слоя глубиной 5—10 мм. Особенностью процесса глубокой цементации является необходимость получения на поверхности деталей повышенной концентрации углерода, что увеличивает перепад концентрации углерода по глубине слоя и повышает скорость диффузии углерода,
При глубокой цементации в поверхностном слое на глубине до 0,5 мм содержится 1,5—2% С, а затем содержание углерода резко снижается и в поверхностном слое на границах зерен наблюдаются грубые карбидные включения. При шлифовании (припуск более 0,6 мм) слой с повышенным содержанием углерода удаляется. Оптимальная температура глубокой цементации 930— 950° С, а продолжительность 50—200 ч в зависимости от требуемой толщины цементованного слоя. Средняя скорость цементации (при получении слоя толщиной 7—10 мм) 0,06 мм/ч.
Рассмотрим процесс термической обработки колец крупногабаритных подшипников из стали 20Х2Н4А. Для цементации шесть-десять колец укладывают (с прокладками между ними) на крестовину и помещают в шахтную печь. После заданной (длительной) выдержки в печи при температуре цементации (930—950° С) кольца вместе с крестовиной охлаждают в масле (во избежание образования карбидной сетки) до 200—300° С (чтобы при охлаждении не происходило образования мартенсита). Затем крестовину с кольцами переносят в печь, нагретую до 550° С, для проведения первой ступени высокого отпуска и выдерживают 8—12 ч. Затем температуру отпуска повышают до 630° С, крестовину с кольцами выдерживают 8—12 ч, охлаждают на воздухе. Цель высокого отпуска — наиболее полное разложение аустенита, сохранившегося (свыше 90%) в цементованном слое после неполного охлаждения с температуры цементации, на феррито-цементит-ную смесь. Качественное выполнение этой операции в значительной степени предопределяет работоспособность деталей крупногабаритных подшипников. Наличие после высокого отпуска остаточного аустенита, образовавшегося при цементации, ведет к сохранению его и при последующей закалке, что вызывает снижение твердости и прочности. После высокого отпуска твердость HRC < 30. В микроструктуре цементованного слоя не допускается наличие замкнутой карбидной сетки и остаточного аустенита.
Затем крестовину с кольцами помещают в шахтную печь для закалки. Температура нагрева 790—810° С, время выдержки 2— 3,5 ч. Охлаждают кольца в масле (вместе с крестовиной) до полного охлаждения или индивидуально каждое кольцо в специальных закалочных машинах. После промывки производят отпуск закаленных колец при 160—170° С с выдержкой 12 ч и охлаждением на воздухе. После закалки и отпуска твердость поверхности HRC 58—62, сердцевины HRC 30—45. Микроструктура поверхностного слоя — скрыто- или мелкоигольчатый мартенсит и карбиды. После шлифования проводят дополнительный отпуск при 130—140° С в течение 7—8 ч с охлаждением на воздухе.
|