Технология переработки нефти и газа. Часть 1Особенности оборудования гидрогенизационных процессов
Основным аппаратом любого гидрогенизационного процесса является ре-актор. В этих процессах применяются реакторы с аксиальным вводом сырья. Они могут иметь сплошной слой, состоящий из одного либо нескольких ката-лизаторов, или быть полочного типа (два – три слоя, с зонами промежуточного охлаждения). Кроме функции обеспечения охлаждения потока по высоте слоя катализатора полочный тип реактора может использоваться для достижения равномерной загрузки сырьем слоя катализатора (как по сечению, так и по высоте).

Внутри реактора чаще всего присутствуют следующие элементы (рису-нок 4.14):
входное устройство (2);
тарелка для распределения потоков по сечению аппарата (3);
один или несколько слоев катализатора (6);
опорные балки и сетки для укладки катализатора;
тарелка (тарелки) для межслойного охлаждения/перемешивания и та-релка (тарелки) для вторичного распределения потока;
гранулированные инертные материалы для оптимизации распределения потока (5);
опорные гранулированные инертные материалы для подстилающего слоя под катализатором (7);
выходное приспособление (9).
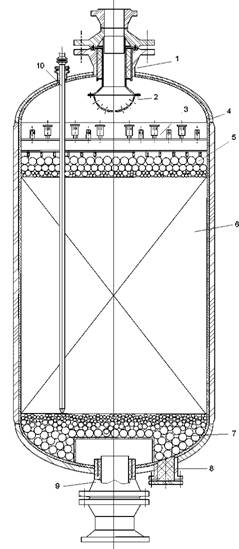
Рисунок 4.14 – Реактор аксиального типа со сплошным слоем катализато-ра, используемый в гидрогенизационных процессах
1 – штуцер входа газо-сырьевой смеси; 2 – входное устройство; 3 – рас-пределительная тарелка; 4 – корпус и футеровка реактора; 5,7 – верхний и ниж-ний слой фарфоровых шариков; 6 – сплошной слой катализатора (или несколь-ких катализаторов); 8 – штуцер для выгрузки фарфоровых шариков и катализа-тора; 9 – штуцер выхода газопродуктового потока; 10 – многозонная термопара
Поток газосырьевой смеси входит в реактор через штуцер (1) и предвари-тельно распределяется по сечению аппарата во входном устройстве (2). Оно необходимо в реакторах и адсорберах для предотвращения струйного попадания сырьевого потока на слой катализатора или адсорбента, в результате чего эти твердые вещества могут быть разрушены или неравномерно распределены в объеме слоя. Однако только с его помощью не удается создать условия для движения потока в аппарате с одинаковой скоростью по всему его сечению. Для этой цели в реакторе устанавливают распределительную тарелку и засыпают поверх слоя катализатора слой инертного материала (фарфоровых шариков). В некоторых случаях перед распределительной тарелкой размещают тарелку для сбора механических примесей, например окалины.
В сплошном слое может быть использован катализатор одного или нескольких типов. Слой катализатора является полезным объемом реактора, именно в нем протекают реакции. Чем он больше, тем ниже при определенной производительности установки объемная скорость подачи сырья, тем больше время контакта сырья с катализатором и тем глубже превращается сырье. Если требуется значительно увеличить глубину превращения сырья (например, при переходе на выпуск дизельного топлива с более низким содержанием сернистых соединений), то эту задачу можно решить (помимо использования более активных катализаторов и высокой температуры процесса) или путем снижения производительности установки по сырью (что экономически невыгодно) или за счет увеличения загрузки катализатора. В последнем случае нередко возникает необходимость монтажа дополнительного реактора. Слой катализатора в реак-торах, как правило, составляет 60-65% от их внутреннего объема. Катализатор в нем должен размещаться так, чтобы в слое не образовывалось пустот и зон с плохой упаковкой. В противном случае газосырьевой поток будет неравномер-но распределяться по продольному и поперечному сечению реактора, что вызо-вет:
необходимость повышения средневзвешенной температуры в слое ка-тализатора для достижения требуемого качества продуктов;
увеличение скорости деактивации катализатора из-за эксплуатации его в более жестких условиях;
усиление нарушений радиального переноса тепла, в результате чего предельно допустимые температуры в реакторе будут достигаться преждевременно;
сокращение межрегенерационного периода работы, повышенный рас-ход катализатора и увеличение времени простоя установки.
Поэтому для эффективной эксплуатации установки очень важно качество загрузки катализатора в реактор и создание условий для равномерного распре-деления сырьевого потока в нем. Равномерная плотность катализатора по слою в последние годы достигается за счет использования специальной технологии к плотной загрузки. Качественное распределение сырьевого потока в реакторе может быть достигнуто путем совершенствования конструкции соответствую-щих внутренних устройств данного аппарата. Например, применением взамен существующих в настоящее время распределительных тарелок новых конст -рукции компании "Shell" с высокой степенью диспергирования жидкости и га-за, в которой используются распылительные сопла. Сравним работу данной та-релки с применяемыми ранее (рисунки 4.14 и 4.15). Распределительные тарелках обычной конструкции сконструированы таким образом, что сырьевой поток вводится в слой катализатора через отдельные выступающие над тарелкой пе-реточные трубки или через отверстия в тарелке. На поверхность слоя под такой тарелкой попадает достаточно крупная струя, за счет чего "смачивается" только зона непосредственно под переточной трубкой или отверстием. Верхняя по-верхность катализатора смачивается всего на 10-20%, а остальная его поверх-ность остается "сухой" и не используется. Такие распределительные тарелки применяются в сочетании с достаточно большим слоем инертного (распредели-тельного) материала.
Колпачковые барботажные распределительные тарелки лишь ненамного лучше. У них "смачивание" верхней поверхности составляет около 30%. По-этому под них также рекомендуется загружать слой инертного материала.
В распределительных тарелках конструкции компании "Shell" внутри ка-ждого сопла образуется высоко диспергированная газо-жидкостная фаза, кото-рая образует широкие и равномерные струи, эффективно покрывающие прак-тически всю поверхность верхнего слоя катализатора. Поэтому при использо-вании тарелок данной конструкции резко падает актуальность использования инертного материала перед слоем катализатора. Высота его слоя сокращается с 0,6 до 0,1 метра. Это позволяет увеличить загрузку катализатора в реактор. В нижней части реактора располагается устройство вывода продуктов реакции. Оно, чаще всего, представляет собой стояк с прорезями, обтянутый нескольки-ми слоями сетки. На него насыпается несколько слоев фарфоровых шариков – нижние более крупные, а верхние мелкие (около 5 мм). Обычно высота слоя фарфоровых шариков составляет 0,6 метра. Он служит в качестве опоры слоя катализатора и, кроме того, улучшает условия вывода газопродуктового потока из реактора. В данной зоне также имеются возможности для увеличения объема загружаемого катализатора. Это может быть достигнуто за счет замены сущест-вующего выходного устройства на сетчатую неглубокую корзину конструкции компании "Shell" и минимизацией толщины опорного подстилающего слоя под катализатором.
Забиваем Сайты В ТОП КУВАЛДОЙ - Уникальные возможности от SeoHammer
Каждая ссылка анализируется по трем пакетам оценки: SEO, Трафик и SMM.
SeoHammer делает продвижение сайта прозрачным и простым занятием.
Ссылки, вечные ссылки, статьи, упоминания, пресс-релизы - используйте по максимуму потенциал SeoHammer для продвижения вашего сайта.
Что умеет делать SeoHammer
— Продвижение в один клик, интеллектуальный подбор запросов, покупка самых лучших ссылок с высокой степенью качества у лучших бирж ссылок.
— Регулярная проверка качества ссылок по более чем 100 показателям и ежедневный пересчет показателей качества проекта.
— Все известные форматы ссылок: арендные ссылки, вечные ссылки, публикации (упоминания, мнения, отзывы, статьи, пресс-релизы).
— SeoHammer покажет, где рост или падение, а также запросы, на которые нужно обратить внимание.
SeoHammer еще предоставляет технологию Буст, она ускоряет продвижение в десятки раз,
а первые результаты появляются уже в течение первых 7 дней.
Зарегистрироваться и Начать продвижение
В результате всего вышесказанного удается увеличить на 20-30% загруз-ку катализатора в существующие реакторы и тем самым появляется возмож-ность увеличить глубину превращения сырья в них без монтажа дополнитель-ных реакторов.
Помимо реакторов к основному оборудованию секции относятся печи. Печи П-301, П-302 – вертикально-секционные с подовым расположением фор-сунок. П-301 состоит из двух секций. Каждая секция имеет радиантную и кон-векционную части. ГСС нагревается вначале в конвекционной камере, а затем в радиантной. Радиантная часть представляет собой металлическую камеру ко-робчатой формы, поднятую над землей на стойках каркаса. Змеевик в радиант-ной камере расположен вертикально вдоль стенок камеры. Конвекционная ка-мера расположена сверху над радиантной камерой и имеет также коробчатую форму.
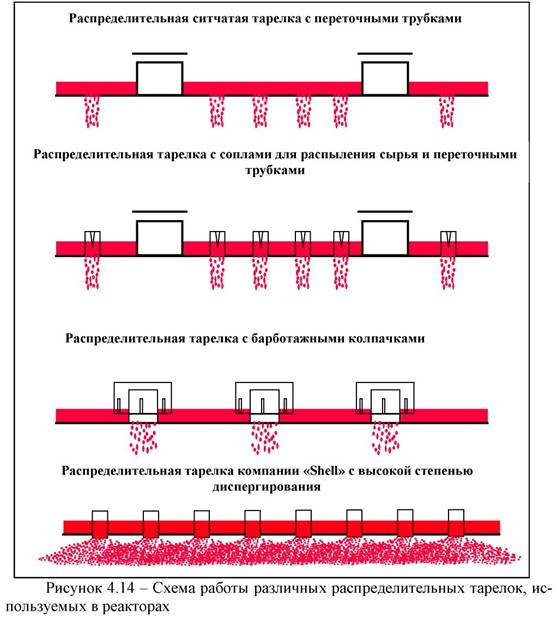
Конвекционный змеевик выполнен из ошипованных труб, расположен-ных в камере горизонтально. Для защиты шипов от воздействия высокой тем-пературы и прямой радиации первый ряд труб змеевика (снизу) выполнен из гладких труб. В обеих камерах над конвекцией смонтирован змеевик газопере-гревателя для нагрева ВСГ, подаваемого в колонну K-30I, или пара-14 в цикле регенерации катализатора. Камеры печи и газоходы футерованы изнутри лег-ким жаропрочным бетоном. Дымовые газы из камеры конвекции поступают по газоходу в котел-утилизатор КУ-201, а затем выбрасываются в атмосферу через трубу высотой 180 м, обеспечивающей тягу и необходимое рассеивание про-дуктов сгорания в атмосфере.
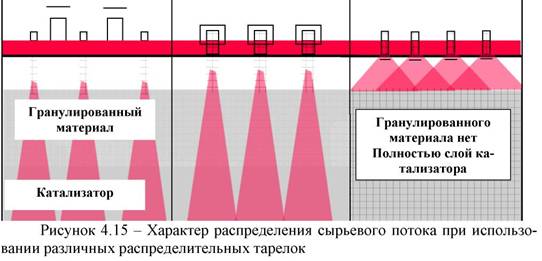
На выходе из каждой камеры конвекции установлен шибер для регулиро-вания разрежения в печи. Каждый шибер имеет ручной и дистанционный при-вод. В качестве ручного привода используется лебедка, установленная на верх-ней площадке печи, разрежение при этом контролируется тягонапоромером по месту. Для дистанционного регулирования разрежения имеется пневмоприбор.
По газодымовому тракту регистрируется:
температура дымовых газов на перевале;
температура дымовых газов после конвекции;
разрежение в камерах.
Продуктовый змеевик в радиантной камере печи – двухпоточный, а в ка-мере конвекции – четырехпоточный. В поду печей установлено по 6 форсунок ГГМ-5.
Топливо печей комбинированное, газо-мазутное. Топочный мазут посту-пает на установку из заводского топливного кольца. Топливный газ к форсун-кам печи поступает из общезаводской сети через сепаратор С-209 и подогрева-тели Т-207,208. В линию топливного газа печи П-301/1 врезана линия углево-дородного газа из колонны К-307 для сжигания его во время остановки печи П-203, где он сжигается постоянно.
Конструктивно печь П-302 полностью соответствует печи П-301 с неко-торыми изменениями.
печь П-302 – односекционная;
радиантный и конвекционный змеевики – 4-х поточные;
в поду печи П-302 – 4 форсунки.
|